Hermetic Compressor Manual
Copeland Copeland Discus From 2, 3 and 8 cylinder semi-hermetic reciprocating compressors for medium/low temperature refrigeration and high temperature applications like process cooling or air-conditioning. The key difference between Discus and traditional reciprocating technologies lies in the valve plate design.
The Discus valve plate allows gas to flow into the cylinders with a minimum heat gain, while suction cavities are designed to smoothly route the gas to minimize losses. Copeland Discus USD.
. Hermetic Compressor Service Handbook Wholesale Distribution North America. Hermetic Compressor Service Handbook Ann Arbor, MI 48108 REV 3/11. Handbook Purpose and Description Tecumseh Products Company has prepared this Service Handbook to assist service personnel in safely installing and servicing refrigeration and air conditioning equipment.
The information in this Service Handbook is generally limited to the compressor and to items and conditions affecting the installation, operation, and servicing of the compressor. General Service Safety Precautions Introduction Trained Personnel Only Terminal Venting and Electrocution Refrigerants and Other Chemicals Compressor Removal System Flushing, Purging, and Pressure Testing for Leaks System Charging Prevention of Water-Utilizing System Explosions Start Capacitor Overheating System Evacuation Follow the Labels Model and Application Compressor Model Number Codes Condensing Unit Model Number Codes. Starting a System with Liquid Refrigerant in the Compressor Control of Liquid Refrigerant Floodback to the Compressor During Operation Accumulator Selection Internal Pressure Relief Valves Appendix The Basic Refrigeration Cycle Example of a Tecumseh Hermetic Compressor Reciprocating Compressor Capillary Tube Sizing Approved Hermetic Compressor Oils Notes.
General Service Safety Precautions Chapter 1. SERVICE HANDBOOK Introduction Tecumseh Products Company has prepared this handbook to assist service personnel in safely working with refrigeration and air conditioning equipment that uses Tecumseh Products Company hermetic compressors.
It is not designed to replace the training required for professional service personnel. Mark and red tag the compressor to indicate that there is a ground fault. Do not recon- nect the power leads. Tape and insulate each power lead separately.
Disconnect power before servicing. Always disconnect power before servicing unless it is required for a specific troubleshooting technique. In these situations, use extreme caution to avoid electric shock. FIGURE 1-1: Compressor FIGURE 1-4: Compressor with (1) protective cover and with (1) protective cover (2) bale strap removed to held in place by (2) metal show (3) hermetic terminal. Failure to properly purge or pressure test a system for leaks can result in serious injury or death from explosion, fire, or contact with acid-saturated refrigerant or oil mists. Follow these precautions when purging or pressure testing a system for leaks:. Tecumseh discourages the use of flushing products and recommends the use of suction line filter-drier and proper oil changes.
If the use of a flushing agent is absolutely necessary, follow the flushing agent manufacturer's instructions. Use a pressure regulating valve and pressure gauges. Commercial cylinders of nitrogen contain pressures in excess of 2000 psig at 70°F. At pressures much lower than 2000 psig, compressors can explode and cause serious injury or death. To avoid over pressurizing the system, always use a pressure-regulating valve on the nitrogen cylinder discharge (see Figure 1-7). SERVICE HANDBOOK Prevention of Water-Utilizing System Explosions In certain water-utilizing refrigeration systems, water can leak into the refrigerant side of the sys- tem.
This can lead to an explosion of system components including, but not limited to, the com- pressor. If such an explosion occurs, the resulting blast can kill or seriously injure anyone in the vicinity. To avoid electric shock, electrocution and terminal venting with igni- tion, do not energize a compressor that has a ground fault. Mark and red tag the compressor to indicate that there is a ground fault.
Do not reconnect the power leads. Tape and insulate each power lead separately. Proceed to Step 2. Do not replace the compressor or energize the system before performing Step 2. Step 2: Check for Water in the System Once the compressor is cool to the touch, open the system process valve slightly to see if any water comes out of the system.
Opening the system process valve while the compressor is hot can cause severe burns from steam coming out of the valve. Model and Application Chapter 2.
SERVICE HANDBOOK Tecumseh Compressor Model Number Codes Number of First Two Release Compressor Digits in Digits of Condensing Variant Application Refrigerant Voltage Family Rated BTU Rated BTU Units (Generation) Capacity Capacity A = 1st In this example (4) total See unit information. AEA4440YXA XC E and G = Evaporative Condensate Units S = Shaded Pole Fan Motor (Celseon) Condensing Unit C = Electrically Commutated Fan Motor (Celseon) X = A holding character, reserved for future use Model Number Codes H = Housed Unit Condensing Unit Features, see chart below The letters I, O, and Q are eliminated Standard Unit. SERVICE HANDBOOK Follow the Labels Tecumseh Products Company compressors have labels and markings with important informa- tion. For your safety and the safety of others, read the labels and markings on the product. Serial Label Information The only source for complete compressor information is on the compressor serial label.
On earlier compressors, the serial plate is usually spot-welded on the upper housing of the compressor. J – September M – December Basic Application Information for Hermetic Compressors Tecumseh hermetic compressors are engineered to do specific air conditioning and refrigeration tasks. Hermetic compressors are designed for a particular evaporator temperature range and a specific refrigerant. Evaporator Temperatures The key specification is the evaporator temperature of the system. Compressor Motor and Component Chapter 3. Line 2 (115 Volt Only - Neutral) Single-phase Compressor Motor Types Ground Tecumseh hermetic compressors contain motors designed for specific requirements of starting Compressor - Unit Ground torque and running efficiency. There are four general types of single-phase motors, each dis- PTC Rela y tinctly different from the others.
Line 1 Run Capacitor Plug-In Run Capacitor PSC Motor Starting Tecumseh Products Company pioneered the Relay development of Permanent Split Capacitor Line 2 Thermal Protector compressor motors. This type of motor elim- Line 1.
SERVICE HANDBOOK Minimum starting voltage for the compressor when it is attempting to start (locked rotor) is listed in Table 3-1. Unequalized system pressure: Head and suction pressures must be equal and not more than the pressures listed in Table 3-2. Refrigeration metering device (cap tube or TX valve) should equalize system pressure within 3 minutes. Hermetic Compressor Thermal Protectors Hermetic compressor motors are protected from overheating by thermal protectors built into or mounted in contact with the compressor motor. See the Electrical Service Parts Guide Book for correct replacement thermal protectors. When firmly attached to the compressor housing, the thermal protector device (See Figure 3-8) quickly senses any unusual temperature rise or excess current draw.
SERVICE HANDBOOK Table 3-3: Facts About Thermal Protectors External Line-Break Thermal Protectors. Currently used on all AE, AK, AZ, TP, TH, TW, HG, RK, RG, RN, and AJ models. Sense motor current and housing temperature or combination thereof. Break line current when tripped. Generally do not protect against loss of charge.
When, by design, no air flow passes over housing, a special “static” thermal protector must be used. Are designed for specific compressors and their intended application. Make no substitutions. Will not protect motor if compressor is operated outside its evaporator temperature range Internal Line-Break Thermal Protectors. Currently used on all AH, AB, AV, AG, AW, VS and most AN, SA and SF models. Sense motor current and motor winding temperature or combination thereof.
Break line current when tripped. Never select a replacement relay solely by horsepower or other generalized rating.
Select the cor- rect relay from the Tecumseh Electrical Service Parts Guide Book. There are two types of motor starting relays used in refrigeration and air conditioning applications: the current responsive type and the potential (voltage) responsive type. Potential Type Relay Supplier Code Designations In recent years, Tecumseh has used an increasing number of potential relays with hermetic compressors. A large number of these have been used on air conditioning applications, but there are also many other applications. Since there are many variations with regard to these relays such as number of terminals, coil group, hot pick up, and mounting position, an explanation of the code numbers should be useful in the field. 16 = 'L' bracket for 'FB' model compressors calibration is 5 to 7% lower 20 = 'L' bracket for Tecumseh Twins = 1½ HP and larger than these values. 21 = 'L' bracket for capacitor box mounting 29 = Flat bracket (Marion) was '14' (under cover) See note on page 22.
Capacitor fail- ure and/or starting winding failure could result. To eliminate this, Tecumseh Products Company start capacitors are equipped with bleeder resistors wired across the capacitor terminals. No start capacitor used in conjunction with a potential relay and run capacitor should be installed without such a bleeder resistor. Run Capacitors Since January 1979, capacitors provided by Tecumseh have contained non-PCB oils or have been constructed using non-PCB impregnated metallized paper elec- trodes and polypropylene dielectric.
These capacitors are protected against case rupture by a device within the capacitor can if failure occurs. The operation of this safety device could cause the terminal end to bulge outward ½”. Table 3-5 on page 25 Identification of Terminal Pins There are several different types of terminals used on the various models of Tecumseh compres- sors. Tecumseh terminal pins may be considered in the following order: Common, Start, Run. To identify the terminal pins, we read the order exactly as we would read a book, that is, we start at the top left hand corner and read across the first “line”.
Fuse and Circuit Breaker Sizing The following information applies to compressor motor branch circuit, short circuit and ground fault protection only. NEC Article 440 Hermetic compressors should be protected in accordance with Article 440 of the National Electric Code which calls for substantially larger circuit breakers than are required for open type motors. Servicing Chapter 4. SERVICE HANDBOOK.
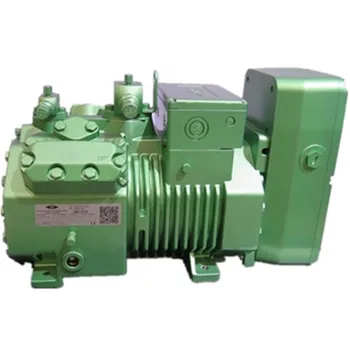
Servicing Introduction to Servicing This chapter provides information to assist service personnel in identifying and correcting com- pressor problems. It provides a general troubleshooting chart that relates complaints or problems to possible causes and solutions.
This chapter also provides greater detail about specific com- pressor problems. SERVICE HANDBOOK Servicing or Troubleshooting Water-Utilizing Systems: Preventing Explosions In certain water-utilizing refrigeration systems, water can leak into the refrigerant side of the sys- tem.
This can lead to an explosion of system components, including but not limited to, the com- pressor. Step 1: Check for a Ground Fault (a Short to Ground) Check the compressor for a ground fault (also known as a short circuit to ground) using the procedure outlined in “Identifying Compressor Electrical Problems” on pages 40-41. If a ground fault does not exist, go to Step 2. If a ground fault does exist, keep the power off.
Hermetic Compressor Pdf
SERVICE HANDBOOK Troubleshooting Chart For your safety, review the “General Service Safety Precautions” (on pages 2-7) before using the troubleshooting chart below. The “General Service Safety Precautions” section provides informa- tion on the following topics:. Trained Personnel Only. Terminal Venting and Electrocution.
Refrigerants and Other Chemicals. Compressor Removal. System Flushing, Purging, and Pressure Testing for Leaks.
Table 4-1: Troubleshooting Chart Complaint Possible Causes Response Compressor will not start - Improperly wired Check against wiring diagram hums but trips on thermal pro- and wire properly tector Low voltage to compressor Turn off system until proper voltage is restored System component, such as Refer to the OEM service thermostat or control/ contac. SERVICE HANDBOOK Table 4-1: Troubleshooting Chart Complaint Possible Causes Response Compressor starts, but does Discharge pressure too high If this is a water-utilizing not switch off of start winding system, see 'Servicing or (continued) Troubleshooting Water- Utilizing Systems: Preventing Explosions' on pages 32-33 Also refer to the OEM service information Internal mechanical trouble in. Table 4-1: Troubleshooting Chart Complaint Possible Causes Response Compressor starts and runs, Return gas too warm If this is a water-utilizing sys- but short cycles on thermal tem, see 'Servicing or Trouble- protector (continued) shooting Water-Utilizing Sys- tems: Preventing Explosions' on pages 32-33. SERVICE HANDBOOK Table 4-1: Troubleshooting Chart Complaint Possible Causes Response Unit operates long or continu- Refrigerated or air conditioned Refer to the OEM service infor- ously (continued) space has excessive load or mation poor insulation, or system in- adequate to handle load Evaporator coil iced Refer to the OEM service infor- mation. Complaint Possible Causes Response Liquid line frosted or sweating System problems such as, re- Refer to the OEM service infor- striction in filter-drier or strain- mation er or liquid shut-off (king valve) partially closed Water leak into refrigerant side of a water-utilizing system System rattles or vibrates dur- Loose parts or mountings, tub- Refer to the OEM service infor. SERVICE HANDBOOK Identifying Compressor Electrical Problems This section describes procedures for checking the compressor’s electrical circuits and compo- nents.
Before doing so, follow the original equipment manufacturer’s service information (OEM) to make sure the system is getting proper voltage and that the control, thermostat, and contactor are working properly. Check for continuity and proper resistance using the pro- cedure on page 42. Why use a megger or Hi-Pot? Tecumseh Products Company recommends checking for a ground fault only with a megger or Hi-Pot. A conventional ohmmeter will not reliably detect a ground fault under certain circumstances. SERVICE HANDBOOK Checking for Continuity and Proper Resistance If no ground fault has been detected using the procedures on pages 40-41, determine whether there is an open or short circuit in the motor windings or if the heater element of the thermal protector is open.
Use the procedure in Table 4-2 to check single- and 3-phase motors. Checking for Other Electrical Problems in Single-phase Motors This section provides procedures for checking the components such as the thermal pro- tector, relay and capacitor in a single-phase compressor.
Table 4-3 (below) can be used to locate the appropriate procedure for the compressor you are servicing. Examine the compressor and determine presence and/or the type of:. Thermal protector (internal or external). Relay (current, potential or PTC). FIGURE 4-2.
Use the letters and/ or numbers on the actual relay to locate the terminals. If replacement parts are needed, refer to the Tecumseh Electrical Service Parts Guide Book for information on proper replacement parts, or call Tecumseh Products Company at 1-800-211-3427. Step 1: Before Continuing with Troubleshooting WARNING! All electric power should be disconnected and you should have already made sure that the compressor does not have a ground fault (see “Checking for a Ground Fault” on pages 40-41). You should have also checked with windings for continuity and proper resistance (see “Checking for Continuity and Proper Resistance” on page 42), made sure the system is getting proper voltage, and that the control, thermostat, and contactor are working properly. FIGURE 4-3. Use the letters and/ or numbers on the actual relay to locate the terminals.
If replacement parts are needed, refer to the Tecumseh Electrical Service Parts Guide Book for information on proper replacement parts, or call Tecumseh Products Company at 1-800-211-3427. Step 1: Before Continuing Troubleshooting WARNING! All electric power should be disconnected and you should have already made sure that the compressor does not have a ground fault (see “Checking for a Ground Fault” on pages 40-41). You should have also checked the windings for continuity and proper resistance (see “Checking for Continuity and Proper Resistance” on page 42), made sure the system is getting proper voltage, and that the control, thermostat, and contactor are working properly. FIGURE 4-4. Use the letters and/ or numbers on the actual relay to locate the terminals.
If replacement parts are needed, refer to the Tecumseh Electrical Service Parts Guide Book for information on proper replacement parts, or call Tecumseh Products Company at 1-800-211-3427. Step 1: Before Continuing with Troubleshooting WARNING! All electric power should be disconnected and you should have already made sure that the compressor does not have a ground fault (see “Checking for a Ground Fault” on pages 40-41). You should have also checked the windings for continuity and proper resistance (see “Checking for Continuity and Proper Resistance”.
FIGURE 4-5. Use the letters and/ or numbers on the actual relay to locate the terminals. If replacement parts are needed, refer to the Tecumseh Electrical Service Parts Guide Book for information on proper replacement parts, or call Tecumseh Products Company at 1-800-211-3427. Step 1: Before Continuing with Troubleshooting WARNING!
All electric power should be disconnected and you should have already made sure that the compressor does not have a ground fault (see “Checking for a Ground Fault” on pages 40-41). You should have also checked the windings for continuity and proper resistance (see “Checking for Continuity and Proper Resistance”. SERVICE HANDBOOK. Prolonged operation on start cycle due to starting load too high. Refer to the OEM service information to use pump down arrangement, if necessary. Excessive short cycling. Short cycling can be caused by problems with the com- pressor’s thermal protector or system components such as the thermostat, control, contactor, or high or low pressure cut-out.
FIGURE 4-6. Use the letters and/ or numbers on the actual relay to locate the terminals. If replacement parts are needed, refer to the Tecumseh Electrical Service Parts Guide Book for information on proper replacement parts, or call Tecumseh Products Company at 1-800-211-3427. SERVICE HANDBOOK Step 1: Before Continuing with Troubleshooting WARNING! All electric power should be disconnected and you should have already made sure that the compressor does not have a ground fault (see “Checking for a Ground Fault” on pages 40-41).
You should have also checked the windings for continuity and proper resistance (see “Checking for Continuity and Proper Resistance”. Step 6: Check Start Capacitor CAUTION: using a 20,000 ohm resistor, discharge the capacitor before removing it from the system to avoid damage to measuring devices and risk of electric shock. Disconnect the start capacitor from the system. Remove the bleed resistor.
Use a capaci- tance meter to measure the capacitance. FIGURE 4-7. Use the letters and/ or numbers on the actual relay to locate the terminals. If replacement parts are needed, refer to the Tecumseh Electrical Service Parts Guide Book for information on proper replacement parts, or call Tecumseh Products Company at 1-800-211-3427.
Step 1: Before Continuing with Troubleshooting WARNING! All electric power should be disconnected and you should have already made sure that the compressor does not have a ground fault (see “Checking for a Ground Fault” on pages 40-41). You should have also checked the windings for continuity and proper resistance (see “Checking for Continuity and Proper Resistance” on page 42), made sure the system is getting proper voltage, and that the control, thermostat, and contactor are working properly. SERVICE HANDBOOK Disconnect the start capacitor from the system. Remove the bleed resistor. Use a capaci- tance meter to measure the capacitance. The capacitance value should be the rated value minus 0% to plus 20%.
If it is outside of this range, then the start capacitor needs to be replaced. FIGURE 4-8 and 4-9. Use the letters and/ or numbers on the actual relay to locate the terminals. If replacement parts are needed, refer to the Tecumseh Electrical Service Parts Guide Book for information on proper replacement parts, or call Tecumseh Products Company at 1-800-211-3427. SERVICE HANDBOOK Step 1: Before Continuing with Troubleshooting WARNING!
All electric power should be disconnected and you should have already made sure that the compressor does not have a ground fault (see “Checking for a Ground Fault” on pages 40-41). You should have also checked the windings for continuity and proper resistance (see “Checking for Continuity and Proper Resistance” on page 42), made sure the system is getting proper voltage, and that the control, thermostat, and contactor are working properly.
to the OEM service information. Vibration due to loose relay mounting. Tighten relay mounting. Use of incorrect run capacitor. Replace with proper run capacitor. Step 5: Check Start Capacitor CAUTION: using a 20,000 ohm resistor, discharge the capacitor before removing it from the system to avoid damage to measuring devices and risk of electric shock. √ The electrical system on this type of motor is shown in FIGURE 4-10.
If replacement parts are needed, refer to the Tecumseh Electrical Service Parts Guide Book for information on proper replacement parts, or call Tecumseh Products Company at 1-800-211-3427. Step 1: Before Continuing with Troubleshooting WARNING! All electric power should be disconnected and you should have already made sure that the compressor does not have a ground fault (see “Checking for a Ground Fault” on pages 40-41). You should have also checked the windings for continuity and proper resistance (see “Checking for Continuity and Proper Resistance”. Use the letters and/ or numbers on the actual relay to locate the terminals. If replacement parts are needed, refer to the Tecumseh Electrical Service Parts Guide Book for information on proper replacement parts, or call Tecumseh Products Company at 1-800-211-3427.
Step 1: Before Continuing with Troubleshooting WARNING! All electric power should be disconnected and you should have already made sure that the compressor does not have a ground fault (see “Checking for a Ground Fault” on pages 40-41). You should have also checked the windings for continuity and proper resistance (see “Checking for Continuity and Proper Resistance” on page 42, made sure the system is getting proper voltage, and that the control, thermostat, and contactor are working properly. FIGURE 4-14. Use the letters and/ or numbers on the actual relay to locate the terminals.
Semi Hermetic Compressors
If replacement parts are needed, refer to the Tecumseh Electrical Service Parts Guide Book for information on proper replacement parts, or call Tecumseh Products Company at 1-800-211-3427. Step 1: Before Continuing with Troubleshooting WARNING! All electric power should be disconnected and you should have already made sure that the compressor does not have a ground fault (see “Checking for a Ground Fault” on pages 40-41). You should have also checked the windings for continuity and proper resistance (see “Checking for Continuity and Proper Resistance” on page 42), made sure the system is getting proper voltage, and that the control, thermostat, and contactor are working properly. FIGURE 4-15. Use the letters and/ or numbers on the actual relay to locate the terminals. If replacement parts are needed, refer to the Tecumseh Electrical Service Parts Guide Book for information on proper replacement parts, or call Tecumseh Products Company at 1-800-211-3427.
Step 1: Before Continuing with Troubleshooting WARNING! All electric power should be disconnected and you should have already made sure that the compressor does not have a ground fault (see “Checking for a Ground Fault” on pages 40-41). You should have also checked the windings for continuity and proper resistance (see “Checking for Continuity and Proper Resistance” on page 42), made sure the system is getting proper voltage, and that the control, thermostat, and contactor are working properly. Is Your Compressor Eligible for Return Under Warranty? Authorized Tecumseh wholesalers are asked to test every in-warranty compressor that is returned to them.
The Tecumseh factory tears down and examines a representative sam- ple of compressors returned by authorized wholesalers and notes the reason for failure. Installation and Replacement Chapter 5. SERVICE HANDBOOK Compressor Tube Connections Tecumseh Products Company supplies compressors to hundreds of manufacturers requiring dif- ferent tubing sizes and arrangements.
Because of this the same compressor model may be found in the field in many suction and discharge tube variations, each depending upon the specific ap- plication in which it is installed. Discharge Discharge Tube Tube Discharge Tube Discharge Tube Discharge Discharge Tube Tube RK, RG FIGURE 5-1 (cont.): Standard discharge tubing arrangements. SERVICE HANDBOOK Refrigerant Line Sizes R-12, R-134a and R-404A Refrigerant Line Sizes for Remote Systems Commercial Refrigeration Refer to Tables 5-1 through 5-8.
The recommended suction line sizes are based on a pres- sure drop no greater than the equivalent of a 1.5°F change in saturation temperature. The resulting pressure drop should provide sufficient refrigerant velocities necessary for proper oil return for suction lines up to 100 ft in length.
SERVICE HANDBOOK. SERVICE HANDBOOK. As shipped with the compressors, the rotolock service valves have a small plastic dust plug inside the threaded end. Be sure to remove this plug before installing. Service valves on Tecumseh systems are “front seated” by turning the valve stem clockwise. This closes the valve and opens the gauge port.
W AR N I N G If a compressor motor failure has occurred, refrigerant or mixtures of refrigerant and oil in the system can be acidic and can cause chemical burns. As always, to avoid injury, wear appropriate protective eye wear, gloves and clothing when servicing an air conditioning or refrigeration system. If refrigerant or mixtures of refrigerant and oil come in contact with skin or eyes, flush the exposed area with water and get medical attention immediately. The following outlines a process for compressor replacement and system clean-up for a system equipped with a Tecumseh compressor. You should refer to the original equipment manufac- turer’s (OEM) service information. SERVICE HANDBOOK Determine Extent of System Contamination Following the precautions in ”Refrigerants and Other Chemicals” and “Compressor Removal” on page 4, remove the compressor.
Use the following guidelines to determine whether contamination, if any, is limited to the compressor or extends to the system. If the discharge line shows no evidence of contamination and the suction stub is clean or has only light carbon deposits, then the contaminants are limited to the compressor housing (Compressor Housing Contamination).
Never use a compressor to evacuate a system. Instead, use a high vacu- um pump specifically designed for that purpose.
Never start the compressor while it is under deep vacuum. Always break a vacuum with refrigerant charge before energizing the compressor. Failure to follow these instructions can damage the hermetic terminal and may result in terminal venting. As always, to reduce the risk of serious injury or death from fire due to terminal venting, never energize the compressor unless the protective terminal cover is securely fastened. Charge the System and Check the Pressure Drop Charge the system and place in operation.
Follow the safety precautions outlined in “Sys- tem Charging” on pages 5-6. Immediately after startup, check the pressure drop across the suction line filter-drier. SERVICE HANDBOOK Table 5-8: Suggested Maximum Pressure Drop (psi) for Temporary Suction Filter-Drier Installation During Cleanup Application Air Cond High Medium Evaporator +55 to +32 +55 to +20 +30 to -10 +10 to -20 -20 to -40 Range, °F R-12, R-134a R-22, R- 404A, R- 1 1/2. Replacing Compressors in Water-Utilizing Systems: Preventing Explosions In certain water-utilizing refrigeration systems, water can leak into the refrigerant side of the sys- tem. This can lead to an explosion of system components including but not limited to, the com- pressor. If such an explosion occurs, the resulting blast can kill or seriously injure anyone in the vicinity. Operation FIGURE 6-1: Liquid refrigerant migration to compressor Chapter 6.
These action photographs (see Figures 6-2 to 6-4) were taken in the engineering laboratories of Tecumseh Products Com- pany. A five ton split air conditioning system was used with a four inch sign glass installed in the compressor housing. FIGURE 6-2: Refrigerant and oil mixture fill sight glass after weekend shutdown FIGURE 6-3: Five seconds after start-up, violent foaming action fill sight glass as re- frigerant boils away taking oil charge with it FIGURE 6-4: More than 60 seconds after start-up, oil level is well below normal operating levels - a condition that is an important factor in compressor bearing wear. SERVICE HANDBOOK Operation Crankcase Heater Prevents Liquid Migration This sequence (see Figures 6-6 and 6-7) shows the effects of an electric strap-on crank- case heater applied to the compressor (also see Figure 6-5). The system was again shut- down for a weekend under identical conditions with the exception that the heater was energized throughout the shutdown period.
12 hours before startup or after a prolonged shut- down. Three types of crankcase heaters are in common use on Tecumseh compressors: wrap-around resistance heater (belly band), immersion type integral heater, and the run capacitance off-cycle heat. SERVICE HANDBOOK Starting a System with Liquid Refrigerant in the Compressor When most air conditioning and commercial systems are started up for the first time each season, a large part of the system refrigerant charge is in the compressor. If there is no crankcase heater or the heat is not operating properly and the unit must be started at the time of the service, then follow these guidelines:.
DO NOT attempt to heat the crankcase by applying a flame to the compressor. Control of Liquid Refrigerant Floodback to the Compressor During Operation Liquid floodback during operation (see Figure 6-9) can be caused by fan failure or dirty clogged filters that can reduce the heat transfer rate to such a point that the liquid refrigerant floods through instead of vaporizing. SERVICE HANDBOOK FIGURE 6-10: Liquid refrigerant enters compressor and settles to the bottom, below the oil. FIGURE 6-11: Five seconds after start-up, violent foaming action fills sight glass as refrigerant boils away taking the oil charge with it. FIGURE 6-12: More than 60 seconds after start-up, oil level is well below normal operating levels - a condition that is an important. Liquid floodback can be prevented by the application of a properly designed and sized suction line accumulator (see Figures 6-13 and 6-14 below and “Accumulator Selection” on page 98).
When properly selected based upon system charge, a suction line accumulator will improve com- pressor reliability and endurance by preventing damaging liquid refrigerant floodback. SERVICE HANDBOOK Accumulator Selection Selecting the proper size is of primary importance. Only one factor need be considered in order to assure the correct accumulator for a particular system - the total refrigerant charge in that system. It is not necessary to know the holding capacity of the accumulator or system variants such as evaporator temperature and capacity in tons of refrigeration. Internal Pressure Relief Valves Certain air conditioning compressors in the AJ, AW, AH, AV, AG, and SF families are quipped with a unique internal pressure relief (IPR) valve. It prevents abnormally high head pressures from devel- oping if a condenser fan motor fails or air passages in the condenser coil become blocked by dirt, leaves, paper, etc.
SERVICE HANDBOOK The Basic Refrigeration Cycle Mechanical refrigeration is accomplished by continuously circulating, evaporating, and condens- ing a fixed supply of refrigerant in a closed system. Evaporation occurs at a low temperature and low pressure while condensation occurs at a high temperature and high pressure. Thus, it is pos- sible to transfer heat from an area of low temperature (i.e., refrigerator cabinet) to an area of high temperature (i.e., kitchen).
The major internal parts of a Tecumseh hermetic compressor are shown in Figure A-2 and are listed in the same sequence as that of the refrigerant gas flow through the compressor. First, the suction is drawn into the compressor housing, then to and through the electric motor which pro- vides power to the crankshaft.
Reciprocating Compressor FIGURE A-2: Internal view of typical air conditioning compressor. (ASHRAE Research Project, RP-948) Example No. 1 Select the capillary required for a Tecumseh R-22 compressor model AEA5460EXA rated at 6,000 Btu/h at 45°F evaporator. Table A-1, we find 13 ft length of 0.064 in capillary tube. 2 Select the capillary required for a Tecumseh R-134a compressor model AJA7461YXA rated at 6,110 Btu/h at 20°F evaporator. Table A-1: continued Capillary Tube, Length - OD Evaporator Temperature, °F Refrigerant Btu/h per circuit 17 ft - 0.031' 18 ft - 0.031' 19 ft - 0.031' 16 ft - 0.036' 17 ft - 0.036' 18 ft - 0.036' 1,000 9 ft - 0.036'. However, since excess oil can also damage compressors, care should be taken not to exceed the oil charge amounts specified.
See “Refrigerant Line Sizes” on pages 76-81. If the correct oil charge is in doubt, please obtain assistance from your Tecumseh Technical Service Representative. Table A-4: Most Common Oil Types to be Used in Compressor Families Compressor Families Source THA THB Naphthenic Witco Suniso 3 GS Witco Suniso 1 GS Lubrax CP-32-RF Synthetic Alkylate (Alkylbenzene) Zerol 150TD Venoco DL-008AS Zerol 150T Venoco DL-008A Zerol 300 SUS Soltex SA56 Lubrax BR-069C-EX Lubrax ALP-415-LCR.

SERVICE HANDBOOK Notes. (also known as a short circuit to ground).
Tecumseh Products Company 1136 Oak Valley Drive Ann Arbor, MI 48108 800.211.3427 734.585.9500 www.tecumseh.com Publication No. TR - 103 ©2011 Tecumseh Products Company. All rights reserved.